Maintenance and Repair Management
The HarmonyERP Maintenance and Repair Module helps your company efficiently manage its assets and production equipment by optimizing planned maintenance processes. It provides quick solutions to potential equipment failures, preventing disruptions in production and ensuring the uninterrupted operation of your business.
The maintenance and repair management module is designed to manage regular equipment maintenance, ensure the rapid resolution of breakdowns, and support business continuity. It includes core features such as periodic maintenance planning, failure management, maintenance documentation, and cost tracking. This module enables companies to maintain effective maintenance operations and contributes to the improvement of operational processes.
It also guides you in planning maintenance and repair support activities. You can easily identify and fully implement the requirements defined by maintenance regulations.
With HarmonyERP’s maintenance and repair management system, your workflows remain uninterrupted. You can take preventative action before issues arise and benefit from a wide range of features to ensure a seamless and efficient process.
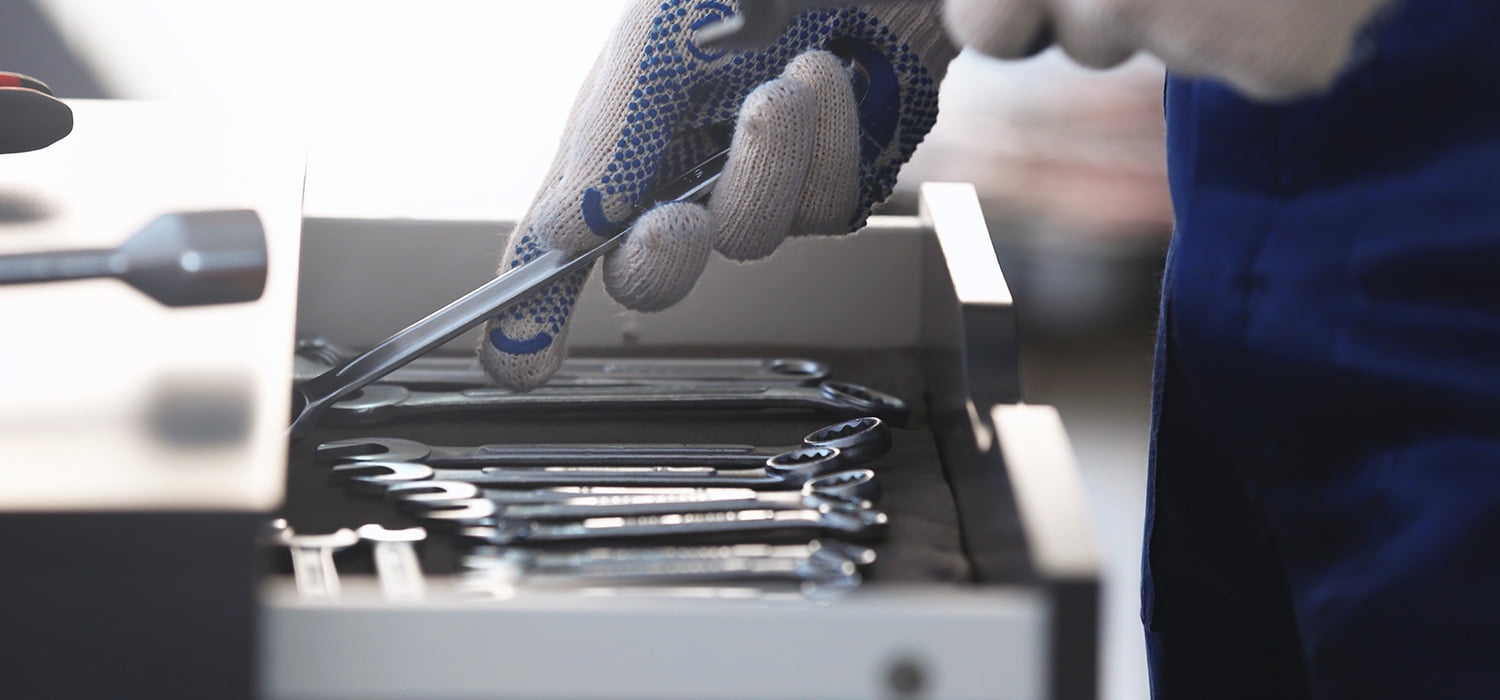
Continuous Maintenance, Reliable Production
With the maintenance and repair management module, we ensure operational continuity by easily performing periodic maintenance and inspections of equipment. Through periodic maintenance and inspection management, fault notifications can be quickly created within the system, allowing maintenance teams to be directed promptly for efficient resolution. Additionally, by tracking maintenance documentation and history, we maintain a clear record of each asset’s past, enabling structured and consistent maintenance management.
Consulting
In addition to our powerful software solutions tailored to your specific needs, we support your business with high-quality consulting and reliable support services.